Optimizing Cost & Performance of Vertical High-Rise Fan Coils
Vertical stack fan coils are a natural and ideal selection for high-rise construction featuring repetitive floor designs - a common design for hotels, colleges, universities, and some institutions. In the past, the starting point for creating a fan coil riser design was a rudimentary process employing a simple pipe flow chart or applying the basic principle of “all risers the same.” Today, there are significant improvements to the design, specification, and installation of vertical stack fan coils. International Environmental Corporation (IEC) leads the industry in developing and implementing improvements in this market.
Redefining IEC Fan coil Risers
During the design phase, valuable opportunities exist to improve riser layout, optimize cost, enhance performance, and simplify installation. Getting this right is essential to an efficient and cost-effective project.
Three Key Considerations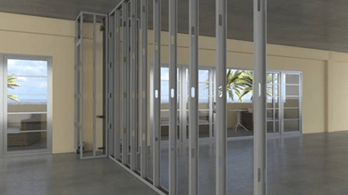
1. Benefit from Independence: One of the first opportunities available for the mechanical contractor is choosing between independent or unit-mounted risers. IEC fan coil units can be manufactured with the riser sections pre-connected, or with the riser and unit separate, allowing first installing the riser sections and then later installing the fan coil units after the risers have been pressure tested and the wall framing and sheeting installed. (SEE PHOTO 1).
There are numerous advantages to installing stand-alone risers first and the units after, including:
Streamlined Distribution: The risers can be shipped to the job before the fan coils, with precise identification tagging. The space required for the palleted risers alone is minimal compared to arriving with the fan coils, and the risers are then readily available for installation in the early stages of mechanical work.
Eye Level Elevation: Risers are ideally connected floor by floor at eye level (5’ above the floor) – either by soldering or through increasingly common mechanical press connections. This installation height avoids working on ladders, a significant safety and productivity advantage for the contractor. The maximum available height of each riser is 10 feet which minimize the need for additional lengths of piping. In the field, risers can be cut to any length for the final connection.
Press Connections: Mechanical press connections, such as ProPress, have established a proven quality and allow for rapid installation without an open flame or the logistical issues of torch fuel tanks for sweating. The labor time per connection is less than 25% of a sweat connection. Combined, this provides a substantial cost and time savings advantage.
Fan Coil Riser Insulation: The riser can be ordered from the factory pre-insulated, providing significant cost savings and reduction in multi-trade coordination. Preparation is essential to ensure the riser insulation thickness is exempted from the unit manufacturing standard, and that the building inspectors are aware, simplifying approvals.
Anchors and Isolation: The risers can be easily anchored, guided, and isolated by suitable support hardware from a specialized vendor, such as Mason Industries – a great partner for these applications. Proper support selection ensures access to the riser is unobstructed and easily verified.
2. Efficient Logistics: Your fan coil manufacturer’s representative can significantly reduce the logistical burden of managing key aspects of the equipment installation, such as:
Order Fulfillment: This is critical to project success. The vendor accurately completing and executing orders will directly reduce on-site labor through ideal sequencing of unit release to manufacturing, and then palletization and shipping from the factory to the site, all sequenced for floor-by-floor receiving. For planning, the vendor partner should know the maximum number of units possible per pallet and the number of units needed per floor – for example, most pallets are limited to six units. Finally, precise and complete identification tagging is essential for the project’s organization, accuracy, and efficiency.
Manufacturing Sequence: Independent freestanding risers should be released for manufacturing prior to the individual unit cabinets. Each riser must be properly specified, fabricated, and labeled to ensure the connection to the riser above is at “eye level” for the installers and that the coil and drain tee connections are located to align with the openings in the fan coil cabinet. If the room includes a cove molding, and the unit includes a molding base, the height must be accounted for during ordering and manufacturing.
Unit Riser Connections: The risers arrive fitted with 1/2" or 3/4” branch tee connections and an isolating ball valve. The dedicated openings in the back or side of the fan coil cabinet align with the riser tee, so the entire ball valve is located inside the unit. The ball valves are fitted with hose-thread
connections – suitable for the flex connections suitable for the flex connector connection to each unit. The condensate drain riser does not require an isolating valve and connects to the bottom of the drain pan through a P-trap, allowing for proper drainage of the condensate pan.
3. Rise to the Challenge: Historically, many riser systems were sized using outdated rules of thumb, with pipe size selection based only on maximum flow rate or desiring a single pipe size for the entire riser. Today intelligent software programs provide flexible and convenient options to optimize risers for different scenarios, such as single-unit applications, back-to-back installations, or the addition of a dedicated hallway or corridor unit to the riser. For example, IEC fan coils offer a superior selection program, which MRG has developed complete confidence in due to years of experience with the software and product.
A few of the important details to consider when selecting riders include the following:
True Velocity: The software recognizes the tube wall thickness and the inside diameter of the copper size selected for the riser - be it Type M, L, or K - and the effect on water velocity and pressure drop.
Flexible Velocity and Pressure Targets: The software program defaults to a 6 FPS target velocity, however, it will optimize pipe size to any velocity desired. The desired velocity may be adjusted based on the application – for example, five-star hotels may hold to a lower velocity to avoid noise, particularly if the unit is in a bedroom. This example is a specific scenario that shows how the program can design for various target velocities. The program avoids a pressure drop exceeding 10’ of head per 100’ of pipe to avoid excessive pressure drop, velocity, and pump energy.
Flow Control: Two-way control valves are typically fitted on every floor, except for the top – to avoid potential thermal isolation of the riser. Each riser set should have an automatic balancing valve on the bottom floor of the piping system, which may be located within the base of the fan coils. Valve selection is critical – for example, flapper-style valves have relatively low Cv ratings. Conversely, full port characterized control ball valves with a high Cv have little authority to balance flow. Individual automatic balancing valves fitted for each fan coil unit are ideal and should be considered for optimal and consistent operation.
Optimized Projects: It is highly beneficial for every project to have an optimization selection program run. This essential step has consistently revealed details and opportunities that, when offered to the design engineer, have proven beneficial to the engineer, contractor, and especially the owner. Optimize every project to capitalize on equipment performance and cost savings. Every project.
Superior Rise Selection Every Project. Every Time
IEC fan coils stand at the forefront of the industry, offering an innovative riser selection process to ensure there is attention to detail and no opportunity is missed. Get in touch with MRG to ensure we run your next high-rise construction project through IEC’s optimization selection program.